UGh! At this point I was pretty upset and couldn’t exactly pin point where things went wrong. I figured it was dirty hands prints or non evaporated alcohol still resting on the shell. As I’d mentioned that there was a little checking (wrinkled paint) around the snaps so after I’d stripped off all the paint back to the base, I also drilled out the snaps on the helmet so there wasn’t going to be any reason for the paint not sticking. I also kept looking at the cans I’d bought and the age of how long they’d be sitting on the shelf. Everything lead back to that base coat of old cream colored paint that used as a base. It was a Rustoleum that didn't want to “play well with others”. I’d had a half empty rattle can sitting around from when I’d painted a mini bike several years back. So after putting in a few hours of careful work I found myself back to the base level again, scrapping off the old paint with lacquer thinner and a scuff pad.
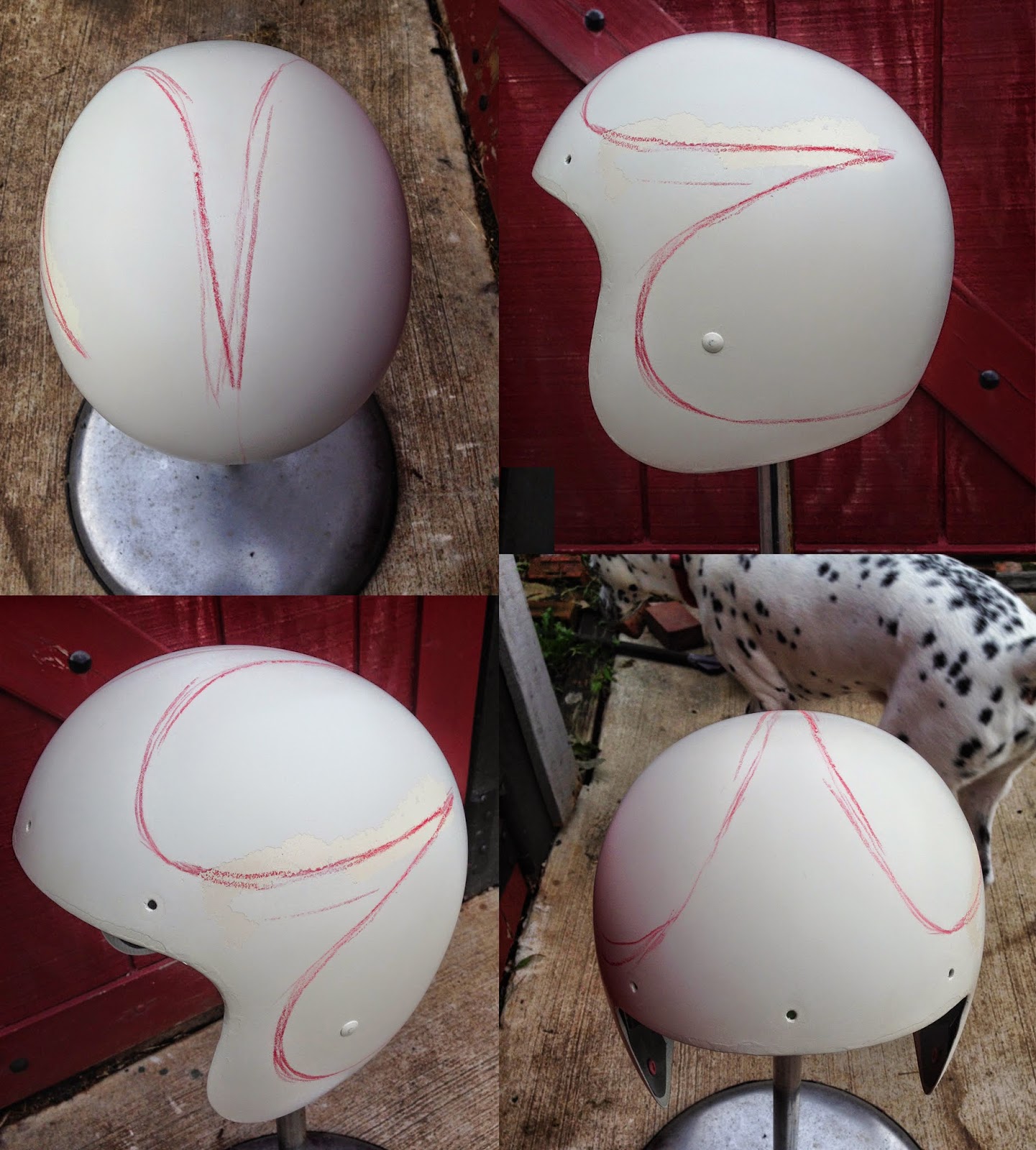
I went to my local painters supply store and bought the red scotch-brite pads, high build primer, 3M painters fine line tape and some more sand paper. There’s nothing worse than starting over again but I’d be damned if I cut corners and wasted time and energy just to have it happen again.
I made sure that the helmet was CLEAN! After the lacquer thinner I washed the helmet with soap and water then re-scuffed it again and wiped clean with alcohol. After it gassed out in the sun and I waited for a low humidity, low wind day, I sprayed again with the high-build primer. Several coats later first with dry spraying for a base to tack to, I laid down wetter coats (basically moving in closer to the target and overlapping the coats more). Another day went by to make sure the coats were dry, I wet sanded again with 600 grit using a soapy mixture with water. It sanded really well and then I re-scuffed again and wiped with alcohol, prepping for the color to go on.
At this point I started to second guess all of what I know about painting, thinking I was going to botch this again. It doesn’t take much to mess with my head when I got sketchy results just prior. From here on out though, everything went quite smoothly!
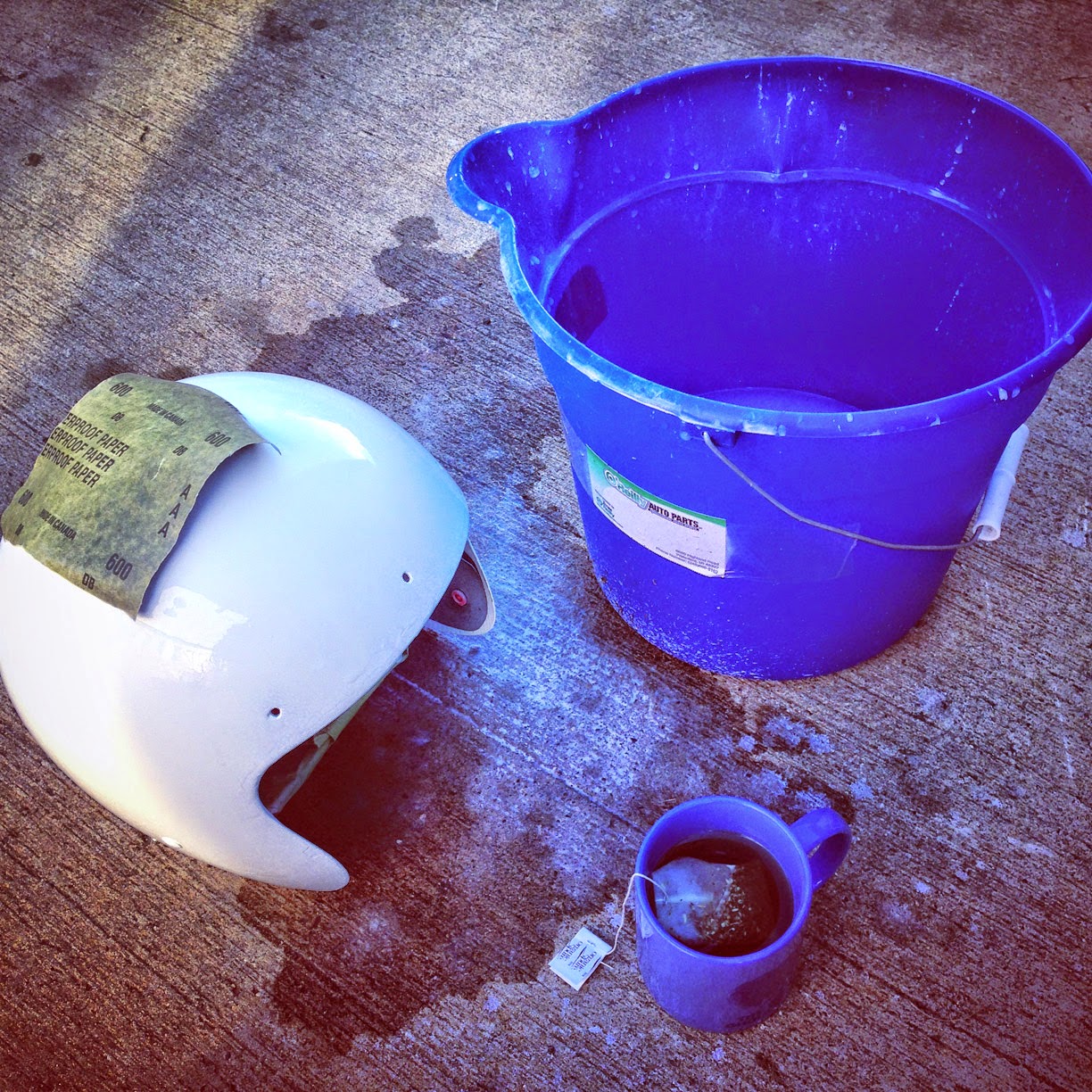
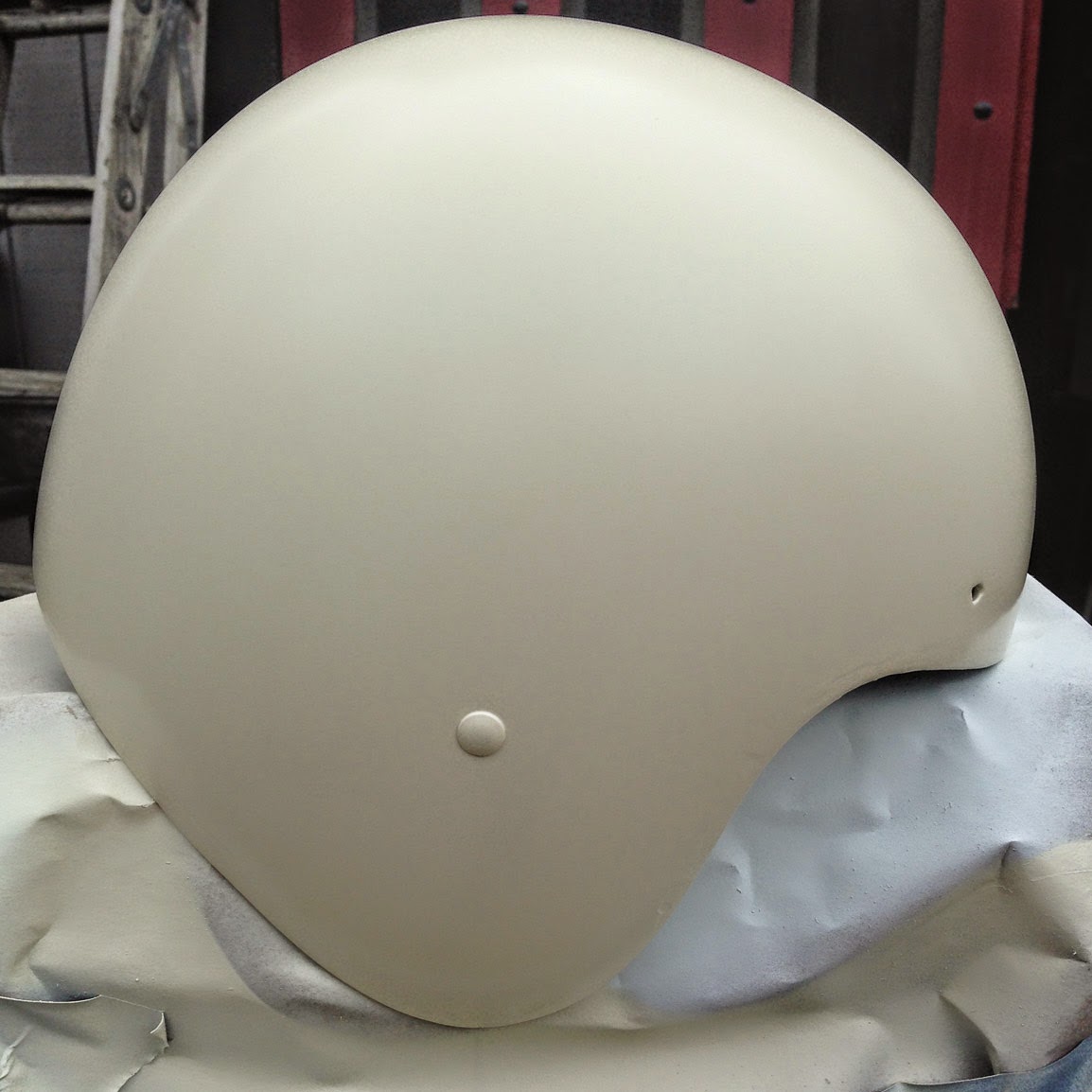
After the Wimbleton white went down (this time I doubled the amount of paint on the base so I could color sand) and it was sanded down and wiped clean, I started with the fine line tape free-handing the curves. The nice part was I’d already sketched out the idea perviously and had the pictures around for reference. I didn’t use any form of measuring tape, I just went by gut and some landmarks on the helmet (snap holes, rivets for the chin strap) and started to layout the tape. Over the years of my silkscreening experience I became pretty skilled at using just my eyes, fingers and gut to line things up. After I’d taped everything off for the new Black pearl I went ahead and did three quick coats on it. The paint looked a lot darker than I recalled and not as blue as I remembered it looked on the car, so despite my previous experience of using old paint, I went back in the barn and grabbed this can of Krylon Stained Glass paint. These stained glass paints only come in the primary colors and are designed to go on glass as a cheap way to achieve the stain glass work. The cool thing about this paint is not only does it spray really nicely, it acts like a candy paint since it’s very translucent but leaves the color tint only without a solid.
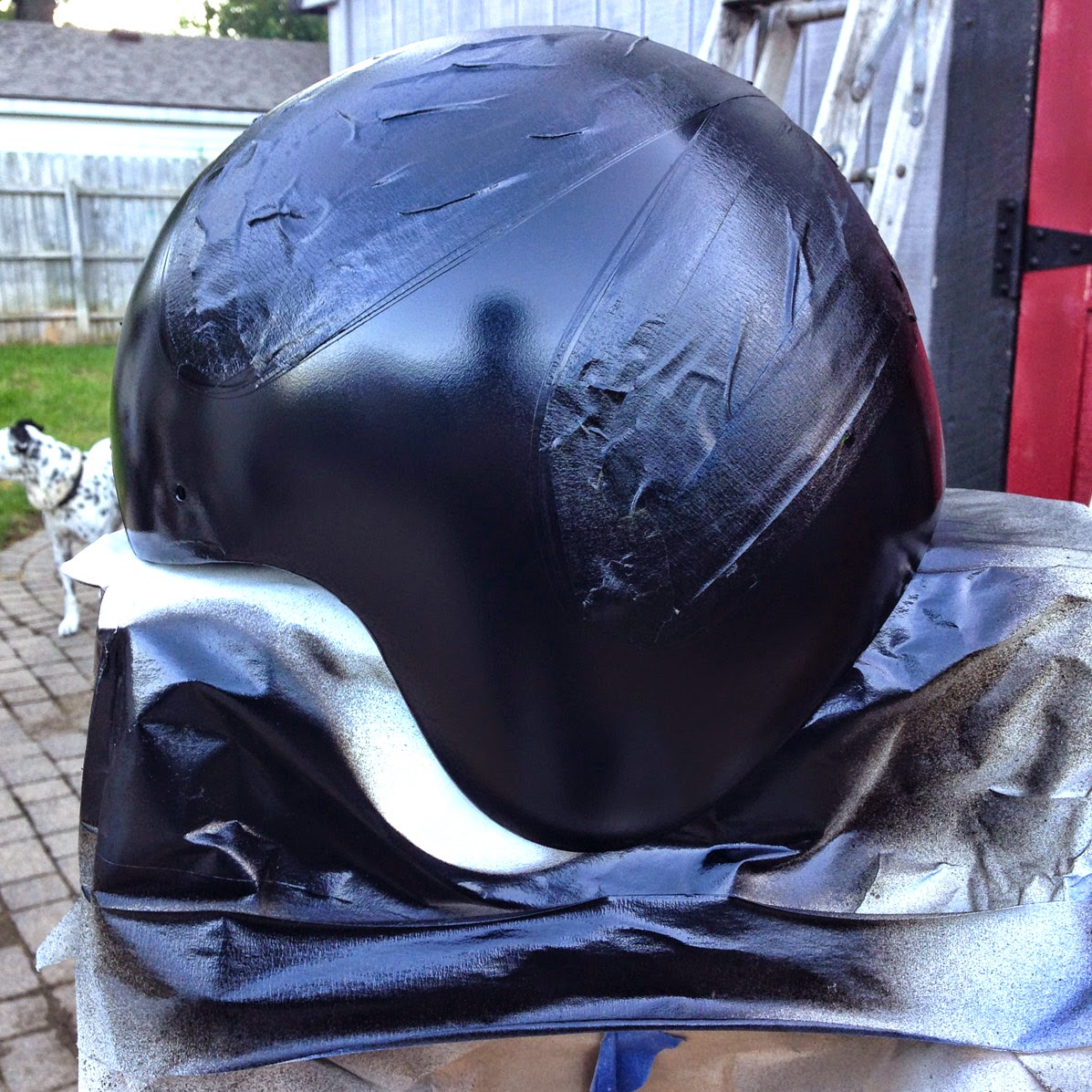
This time around I’d started a test panel always squirting the panel first, then the helmet to make sure all the paints react well with each other. So I wasn't going to coat with this old paint without testing it first. Since most of the checking happens pretty quickly, I would know if it was going to work or not. It coated very nicely and looked great on the panel so I gave it a quick couple coats on top of the Black pearl.
After letting the paint dry for two days, just to be sure, I carefully razored all my tape lines so that when I pulled the tape, I wouldn’t also pull the paint! I’m not 100% positive that it needs to be done with all paint, but I’ve had some unhappy results when I didn’t do this in the past, so I always razor it with color splits
After all the paper and tape were off I was very happy with the symmetry of the scallops. The next thing that needed to happen is to start laying down the base level clear coat to build up the difference in layers of paint as there was a clear step with the three extra layers of paint between the white and black. After layering up two, 8 once cans worth of clear I started wet sanding again, this time with 1200 grit. I should have started with different levels of sand paper (600, 1000, 1200, 1500, 2000), building up, but I was using only with what I had on hand.
It now came time to add a little pinstripe around the color split. Though the colors split nicely, there’s always a little spill over or inconstancies of the tape lines. In my case, I had nice lines, but a little bit of color spill from the blue-black to the white, so a nice little line would cover it up. I had the idea after I removed the snaps that I would be replacing them with brass snaps to give it a custom look rather than just putting the originals back on. So for the accent stripe I thought a metallic gold (which looks more like brass than gold) would work well.
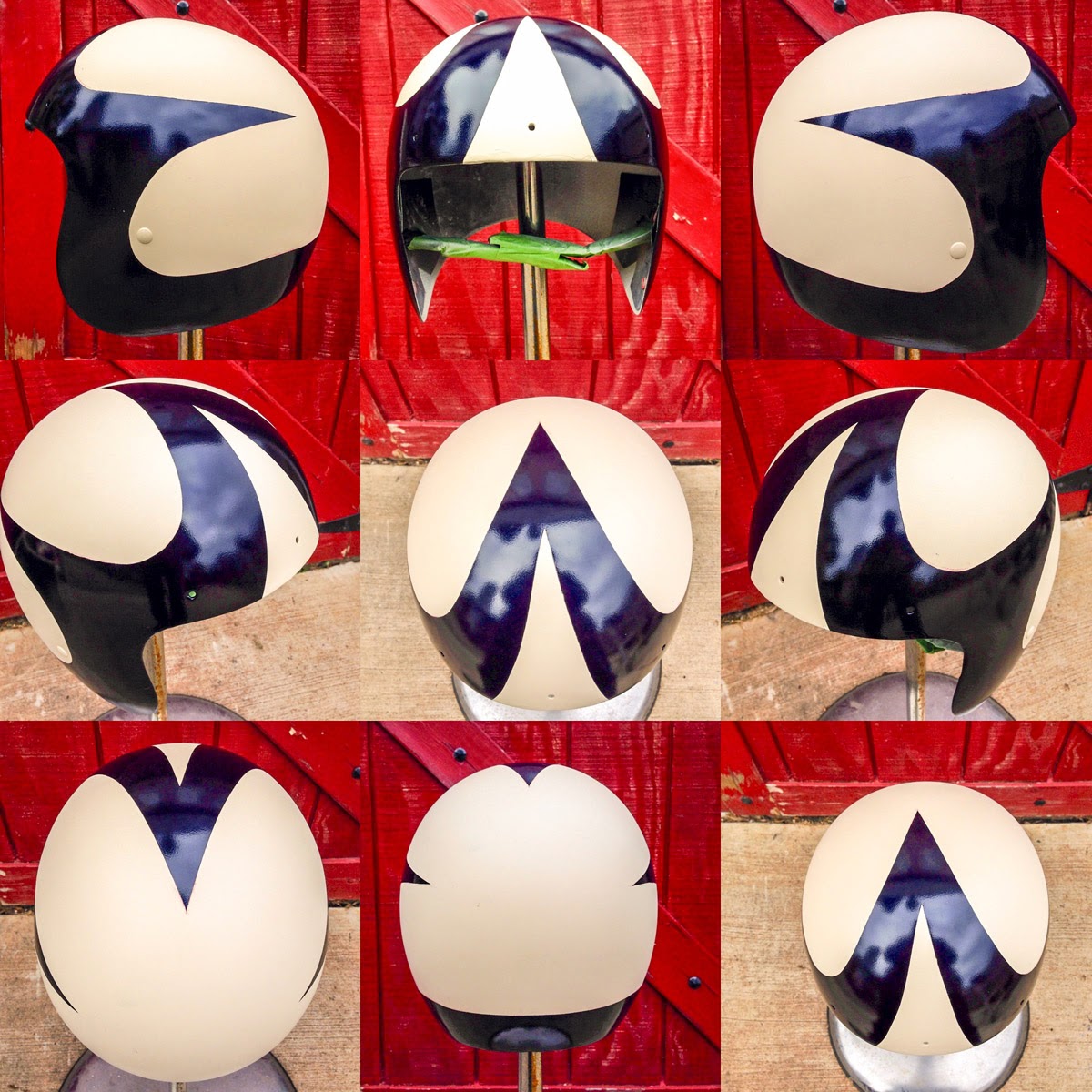
Despite what I’m sometimes called on to do in the art world, I’m not a pinstriper. I know some very talented guys with steady hands but it’s not a skill I’m comfortable with. I did do a couple of attempts with the 1 Shot Metallic gold but I wasn’t happy with how thick I was doing my lines. So instead of coming this far and screwing it up, I consulted my buddy Lil Mark who’s a talented fabricator and pinstriper and had him lay down the lines. Many strippers don’t like the metallics because they are always thin compared with the solids. So Mark’s trick was adding a few drops of black to the mix to give it an antique brass color and also thicken it up a bit.
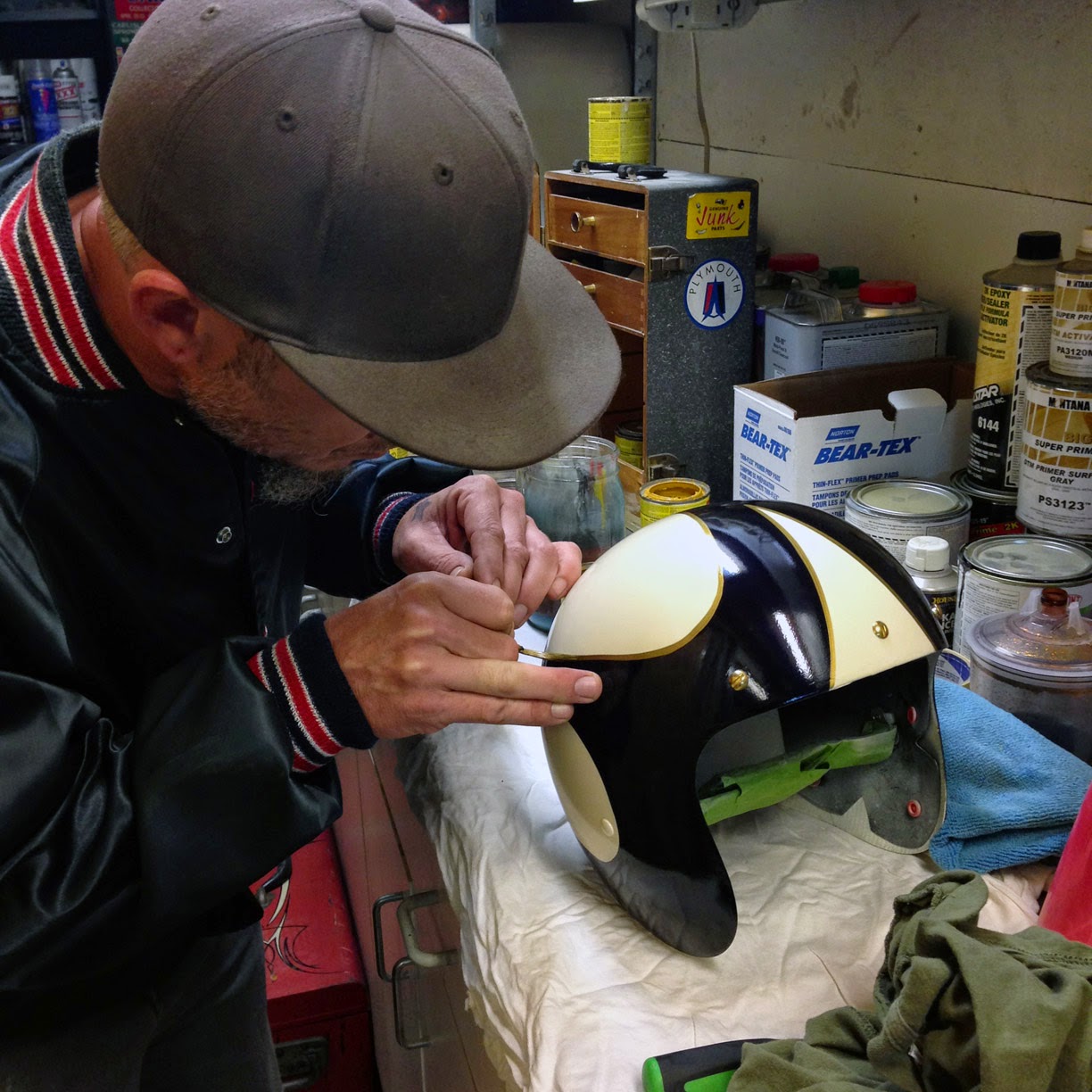
After the lines went down I wanted to clear coat it asap before something could go wrong. Now, since I had been doing my test panel first then the helmet, I didn’t have that same paint on anything other than the helmet. There was a bit of a happy accident with the gold as it got an interesting texture to it under the clear. It’s very fine, so unless you are looking for it, it’s not really noticeable, but I like how it brings a human side to this. It almost gives a gold leaf look to the project.
I ran two more thick coats of clear on top of the helmet. After the second coat of clear I saw a bit of fogging happening which is a pretty good idea to stop as it means there’s too much clear and it’s going to start doing weird things from there if you don’t stop laying it down and you end up with a mess. I also had to change brands of clear from the Duplicolor to Rustoleum but in all my tests it worked fine.
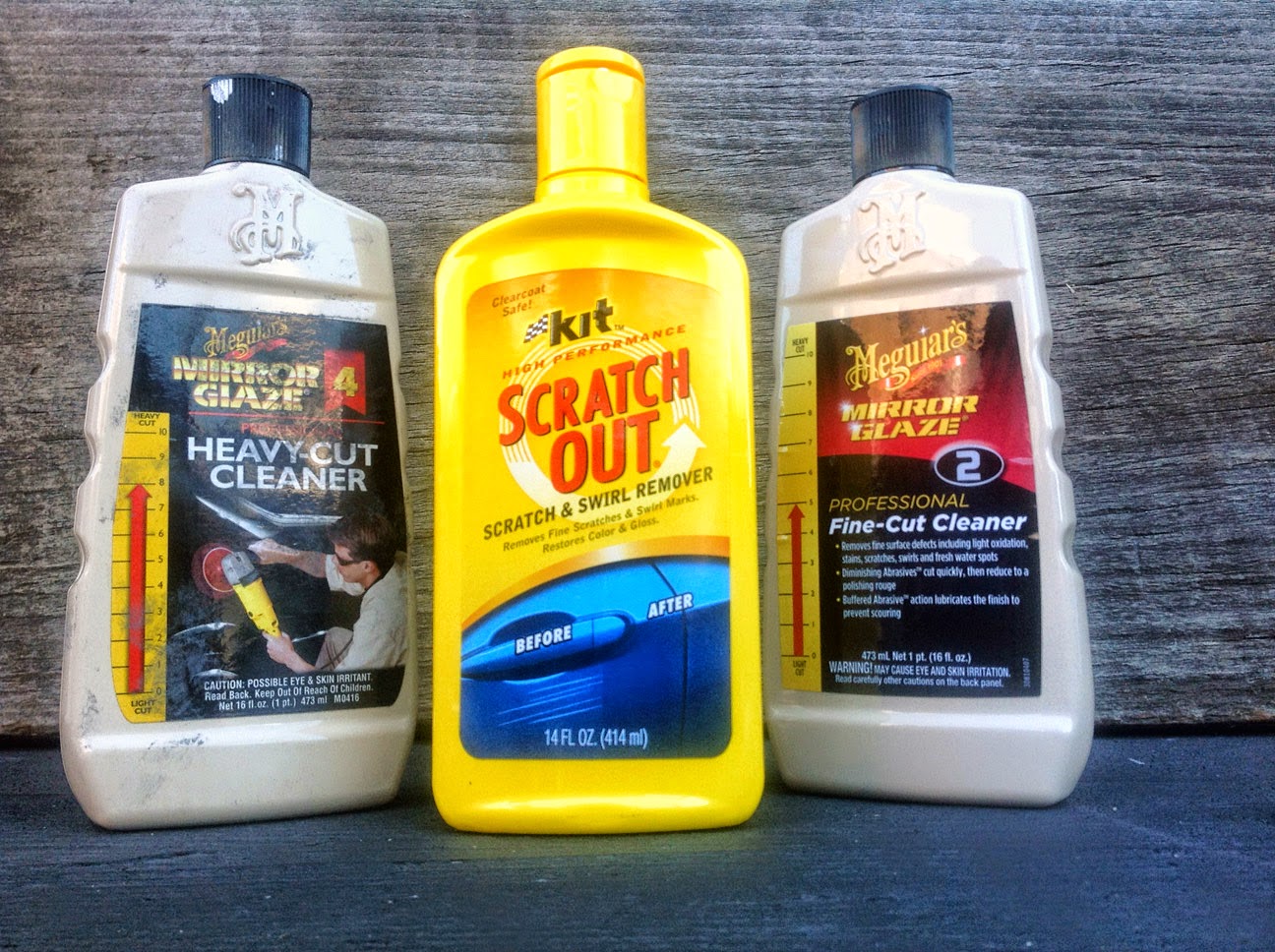
The last step 36 hours after the clear coat went on was the last wet sanding with 2000 grit and soapy water. I did a light cut with that, knocking back the majority of the orange peel texture to it and then moved on to rubbing compounds. I watched a few youtube videos of people doing a cut and rub and learned a little more than what I already knew. I hadn’t considered the difference in the nap of the towel or the pad making a big difference. So with the heavy cut, I started with a terrycloth pad and rubbed and wiped down, then did the same heavy cut with a finer towel. I did the same two steps with the fine cut compound, one with the terrycloth pad and again with the finer towel. The last step was with a scratch remover compound that you can buy at many auto stores designed to take out light scratches and swirls in the clear coat on a car. This went on and came off with a microfiber towel.
THE FINISHING TOUCHES:
To make this helmet more custom I’d mentioned that I wanted to use brass snaps instead of the typical Nickel plated silver snaps. Now, the issue was finding some solid brass snaps. Most seem to not be made of actual brass but rather a coated version of them. I know that military snaps are often solid brass but doing some research on them I realized that I would need to order packages of 100 snaps in most cases to get just a handful needed.
I ended up buying a 10 pack of ‘antique brass’ snaps off of eBay for a few bucks. These aren’t full brass but look correct over a solid gold appearance of the other ones listed as brass. I wanted to match the pinstripe look with that hint of black in it and the antique brass ones looked about perfect. I had this idea of how to attach them using ‘Chicago Screws’ sometimes they’re called post screws or binding or blind screws. Basically two fit pieces that cup together with a space between for a solid object. The cap of the screws only came in one size so I knew that the cap needed to be milled down about 1/8” all around to slide inside the cup of the snap post.
My buddy Eric is a talented artist and clock maker who gave me a hand in turning these screw heads down to the proper size. It worked out perfect! I got a great fit and a great custom look! It’s always handy to have a friend with a truck and even better to have a friend with a lathe! On the front snaps I had to take about 1/16” off the post side to make sure there wasn’t any slop in the snaps which I did with a quick grind on my bench. After getting them in, it was time to do the new edge trim.
I’d recently picked up an office chair at a thrift store for $2 and rebuilt it combining three old chair parts together. I’d asked a friend about how he was redoing his helmet trim and got turned on to RV suppliers who sell edge trim. It’s really easy to use and a great way to customize after you paint. It comes in a few standard colors: Black, Brown, Gray, White and Off-White. Custom colors can be ordered but you have to buy spools of 100’ or more for custom. Having some extra on hand from another project I liked the look and contrast of the off-white color, I decided to use it on this helmet, again, giving it that custom touch over the standard black. It takes approximately 3.5-4 feet to do a standard 3/4 helmet.
Edge-Lok just pushes on; there’s no need for glue or the like because of the nature of how this is constructed. It grabs and holds once in place and is very durable. I did discover if you want to re-dye it, the Duplicolor interior spray dye does an awesome job and available in some loud colors too. Very durable product from what I can tell from a test.
The last step in this actually happened right before the wet sanding of the clear. I had the idea to add a goggle strap to the back. Since most helmets no longer have these straps, and I actually wear goggles on longer rides, I needed to drill a hole. I added two layers of painters tape to the outside of the helmet before marking and drilling as I had a fear that I’d crack, chip or gouge out the clear coat. I don’t know if this is 100% necessary but I like to do this to be safe. Using a Dremel tool on a low setting I made a small hole and then used a rattail file to bring it up to 1/4” needed for the Chicago Screw/Snap combo.
The last step was the strap itself. Most helmets use vinyl for the straps which looks cheap to me. I wanted to use leather, but white leather is harder to come by. There is a bleaching process that can be done to leather to make it nearly white which would work well but all I needed was a 6” long by 3/4” wide piece, too much work for such a small piece. I got the idea while out thrift store shopping. I often look at men’s belts because you sometimes find nice, top grain, full leather belts for a couple bucks. I never made the connection until I was planning this project and new I wanted a white leather belt. So I hit the women’s section and found a few, but only one all leather white belt for $2.
Having done some leather work in the past the first thing I new I wanted to do to this belt was soak it in water because leather shrinks when wet, especially this bleached out leather. This is probably one reason most helmets have vinyl goggle straps to prevent them from shrinking. Since there is a good chance that the helmet will get wet in the elements, I thought it would be a good idea to preshrink the leather so it didn’t happen later on and never be able to be snapped again because it shrunk. To do this, simply get a bowl that will hold the belt coiled up and boil some water. Place the belt in the bowl and pour the water over the belt until it submerged. I recommend keeping the bowl in the sink incase you have spill over. In my case the belt shrunk in length and width so it only needed a little trimming and two holes punched and the snap cap put together to complete the strap.
20 TIPS FOR SPRAY PAINTING FROM A CAN:
I’m by no means an expert but I’ve spray painted a lot of junk over the years. Most of what I’ll list here are common paint tips, but apply to this project as well.
- Wash your hands! Keeping your oils off the project is key to adhesion of paint. Wear powder-free rubber gloves when handling your project. Keep your project clean. Not just oil free, but dust free as well.
- Back tape the edges of your work with painters tape. This will allow an easier transition of the paint and what you are painting on not to stick together and ruin your project. It will also allow you a place to place your fingers if you need to pick up or move your project.
- Elevate your project. If it’s possible to get your project to an area you can walk around and comfortably shoot at from an upright position, you will have much greater results. I recommend saw horses or a step ladder in an open area. Keep in mind that most spray paint cans are designed to work in a vertical position only.
- Keep a consistent distance from your subject. Always try to stay the same distance away when you make your results from tip to topic. If some areas are hard to reach, do some practice motions without spraying so you know if you need something to step on or whatever to stay consistent.
- Don’t use old paint! It cost me a lot more in time than money to just buy a fresh can. Take your time and test everything before you get in a hurry to lay it all down.
- Wipe your project down with alcohol before you paint, let it gas out before you spray (about 10-20 minutes to evaporate). This is basically true for every color change, scuff or between long periods of 24 hours or more with coats.
- Follow the instructions on the can. They are usually right but give very general specs based on a wide range of conditions. If it’s hot, you probably need less dry time and cold, you’ll need more.
- Shake the dang cans up! Don’t forget to give a good shake. If you’ve been spraying for 30 seconds or more consistently, you probably need to give it a quick shake before starting again. When the can gets low, it can “spit” at your project. Stop using that can if it’s spitting as this causes more problems than it helps.
- Do a test panel! I highly recommend having a piece of scrap sheet metal or plexiglass that you can test all of results on before screwing up your project. This will allow you to see what the paint will do before you paint your topic. Do all the same steps as you would with your project with prep and treatment. If you do all the steps, side by side, first on the panel, then on your project, you may be able to see where things went wrong before messing up your project. Use this test panel if you’re the kind of person who likes to test to see if the paint is tacky with your finger.
- Do light coats at first and let them just set up a bit before the next coat. After a tack coating is done, use wet coats (move in a little closer to the topic) Example: If your light, tack coats are are 10-12" away, your wet coats will be 6-8" away from your project.
- Keep a “wet edge” . Overlap your coats moving either left to right or up and down. Don’t let it drip or sag if you can avoid it. It can be fixable, but you'll spend a lot more time and energy sanding than if you were careful to begin with.
- Between coats of paint, invert the spray can and discharge until it’s just air coming out. This keeps the nozzle clean and ready for the next use. This is pretty important step. Some spray paint cans will print this info on it, but many do not. It makes a world of difference to blow out what is in the tip.
- Make sure your paint and your thing you are painting are the same temperature for color paints (see tip #15 for clear). I’ve had some weird results if either your paint or your project are different temperatures. Paint when the temperatures match whats on the can suggested temps and when the humidity and wind is low. If your project is airing out in the sun, move your rattle cans to the sun. If you take your project back to the shade to paint, do the same with the spray paint as well.
- Paint in the shade if you can, not in direct sunlight. After the paint begins to set up (10-15 minutes), you may move it to a sunny spot to dry faster. Remember to rotate the piece so it gets sun all over .
- Clear coat goes on better when the can is warm. To make the can warm, either place it in the sun directly and rotate it or place the can in a warm bucket of water. It goes on much smoother than if it’s cold.
- If your neighbors are mowing the lawn or something that can kick up dust and debris, don’t paint! Or if they start to mow the lawn after you just laid down a layer, move it inside somewhere so it doesn’t pick up crap in the paint. If you should get debris in your paint (like a bug, dog hair, etc) I recommend waiting to remove it when the paint is dry vs. wet as it can be easier to tackle with sanding when dry. I've had some success with tweezering out a rouge dog hair when it's jutting out of fresh paint, but if it's laying down and you start messing around with it, you cause more harm than good.
- Scuff between color changes with a red scotch-brite pad and clean after first with soap and water, then with alcohol before the next coat. If you color sand both colors of paint there is a risk of some bleed over between the colors. The solution is to build up clear coats and sand those so there is less of a step between the layers.
- If you can paint inside or a garage or larger space, make sure it’s well ventilated. Mask off areas you don’t want painted as spray paint can really travel.
- Lay down enough layers (minimum of three good coats) before sanding, otherwise you will sand right through it.
- When doing a color split, I recommend lightly razoring your edge between the paint and the tape so when you pull the tape it doesn’t pull or crack the paint. No need to push hard, a simple scoring of it should suffice.
SANDING/BUFFING TIPS
- When wet sanding, use warm water with a mild soap. A good choice for soap would an automotive wash, not a scented hand soap/sanitizer/etc.
- No need to “push” when sanding, keep it light and let it glide over your paint. Keep the paper and your project clean. If the paper gets debris in it, throw it out. Keep the water clean. Sand in an X pattern for best results. Keep in mind how much clear coat you put on before grinding it down. If you go through, you’ll be starting again.
- Buffing with compound using a variety naps in towels can give different results. Work from large naps to fine naps, ending in micro-fiber towels. Make sure the compound you buy can be used by hand as some are formulated for machine only.
ONE LAST TIP:
Painting can be expensive, but some things can be bought cheap. Hit the dollar store for disposable items like drop cloths, masking paper, alcohol, terrycloth hand-towels, rubber gloves and the like. You can save a lot of money on things you toss away if you buy smart.